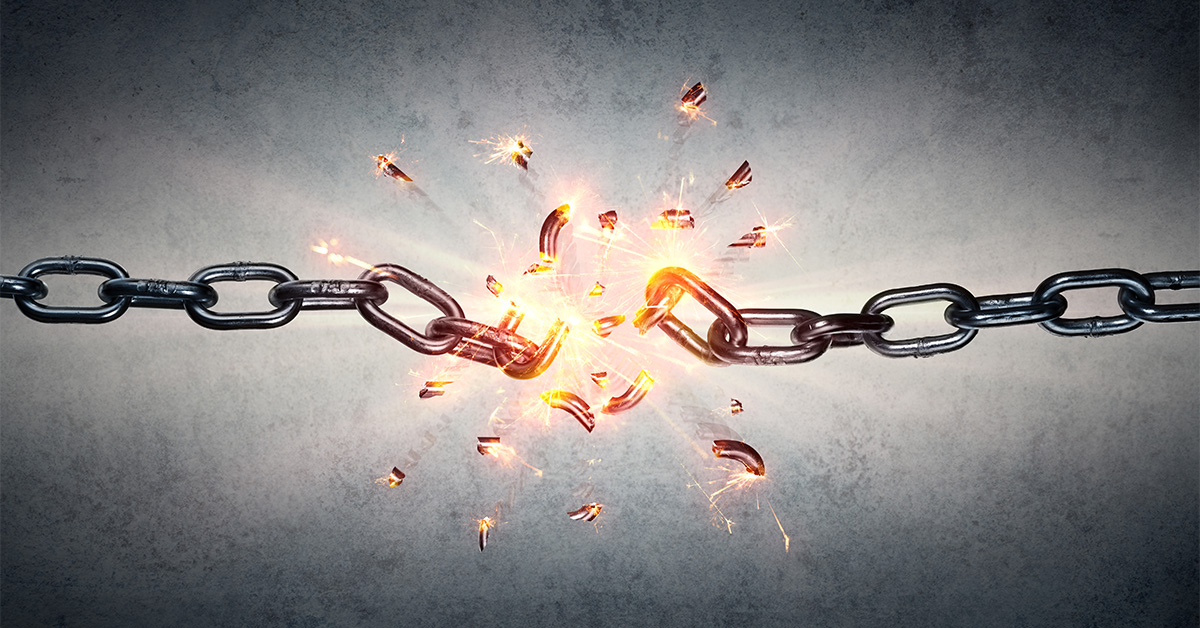
Don’t Let Supply Chain Disruptions Slow You Down
Supply chain disruptions can be a headache for even the most experienced manufacturers and supply chain managers. Within the past few years, there have been many instances where disruptions have been out of most people’s control. This is why it is always important to have redundancies and plans in place for unpredictable events to create resiliency within your supply chain. Resiliency keeps your production line moving no matter the obstacle.
In the manufacturing industry, the supply chain encompasses every step of the process from making products to eventual delivery to customers. This process can look like gathering raw materials, creating, or assembling products, order fulfillment and sales, product delivery, customer support, and account management. Supply chain managers oversee every step of this process to ensure efficiency and prevent supply chain disruptions. In this article, we will discuss what supply chain disruptions are, how they occur, and strategies to maintain a healthy and sustainable supply chain.
Understanding Supply Chain Disruptions
Supply chain disruptions are interruptions in any of the steps listed above. This includes any person or product that is associated with the production, sale, and distribution of goods at any part of the process. For example, you could experience shipping delays, shortage of certain materials, transportation delays, labor shortages, infrastructure failures, and congested ports. Any congestion, otherwise known as bottlenecks, can cause delays and higher production costs for your business. This is especially true if you are reliant on materials coming from different countries.
Supply chain disruptions used to be more localized, which made them easier to prepare for and fix, but with the rise of global suppliers and customers, disruptions are becoming more widespread. These disruptions often lead to shortage of goods, skyrocketing prices, plant closures, lost or untended shipping containers, and eventually an impact to the nation’s economy.
In the day and age of instant gratification, it has become even more imperative to stay efficient and on top of your game.
Causes of Supply Chain Disruptions
Supply chain disruptions can be caused by various internal or external factors. For example, the large container ship, the Ever Given, got stuck in the Suez Canal for six days in March of 2021. Though this may seem like not a huge disaster, it cost nearly $10 billion in trade a day and affected numerous supply chains.
Other common causes include cyber-attacks, security issues, financial instability, transportation and logistic problems, human error, political instability, and natural disasters. The severity of these disruptions determines how long their effects will last.
Severity Levels
Low severity: short-term issues that can be quickly resolved by managers once the issue is identified. This is the easiest of the disruptions to overcome.
Medium severity: disruptions that impact a business for weeks to months, usually due to external factors beyond the control of managers and owners.
High severity: long-term impacts lasting months to years, with significant financial consequences, potentially affecting the long-term viability of companies.
Healthy Supply Chains
A core element of a healthy supply chain is having supply chain orientation. This involves a shared value and belief system aimed at strategically managing supply chains, integrating, synchronizing, and converging operational activities and strategic capacity. Recognizing the importance of supply chains and their flows is the first step.
A healthy supply chain addresses both internal and external issues, creates strategies for future challenges, and focuses on stability to help businesses adapt to external changes. This ensures customer satisfaction and maintains steady profits despite potential disruptions.
Proactive Measures for Supply Chain Resilience
Even with proper planning, supply chain disruptions can still occur. It’s essential to know how to respond when disruptions happen, especially when they are outside of your control.
Creating a healthy and resilient supply chain starts with first observing and gaining a deep understanding of your operations. Identifying risks, collecting data, and developing a business continuity plan to maintain production are all a part of creating a strategic prevention plan.
Implementing backup plans or redundancies for vulnerable parts of the supply chain is crucial. This will give you an advantage to get ahead of issues and increase efficiency. Redundancies are the most effective way to build supply chain resilience.
Having a strategic plan, backup options, and a knowledgeable approach deeply rooted in how your business operates, can significantly mitigate the impact of supply chain disruptions.
Conner Packaging Keeps Your Production Line Moving
Conner Packaging is a leading provider of industrial packaging and foam solutions in the United States. We specialize in custom pallets, crates, and integrated packaging, along with a variety of tailored services for our customers. With 17 plant locations across the country, we have redundancies in place to prevent supply chain disruptions from affecting our customers.
In 2018, Hurricane Michael caused extensive damage to our Panama City location. By shifting orders to nearby plants, we maintained our supply chain while supporting our Panama City plant and employees in their recovery.
Supply chain disruptions are inevitable, partner with a supplier that prepares for the unexpected.